Introduction
Wood-Plastic Composite (WPC) is a revolutionary material in the construction and design industry, offering a blend of wood and plastic properties. Its appeal lies in sustainability, durability, and design flexibility. Understanding the core production and application criteria is crucial to unlock its full potential.
WPC’s reliability and performance hinge on adherence to these essential prerequisites, covering material composition, mechanical attributes, environmental sustainability, and safety standards. Whether you’re a builder, architect, or homeowner, recognizing and following these guidelines is vital for project success.
Our comprehensive guide explores WPC’s fundamental requirements, encompassing material composition, strength, moisture resistance, and compliance with industry standards. By the end, you’ll possess the knowledge needed to make informed choices and leverage the versatility of Wood-Plastic Composite in your projects.
Click to read our article: What is composite decking? pros, cons, and installation process
Material Composition of Wood-Plastic Composite (WPC)
Wood-Plastic Composite (WPC) ‘s material composition is the essence of its innovation. It’s a unique combination of natural wood fibers or flour and thermoplastic resins, combining the best of both worlds to create a versatile and sustainable material that has revolutionized various industries.
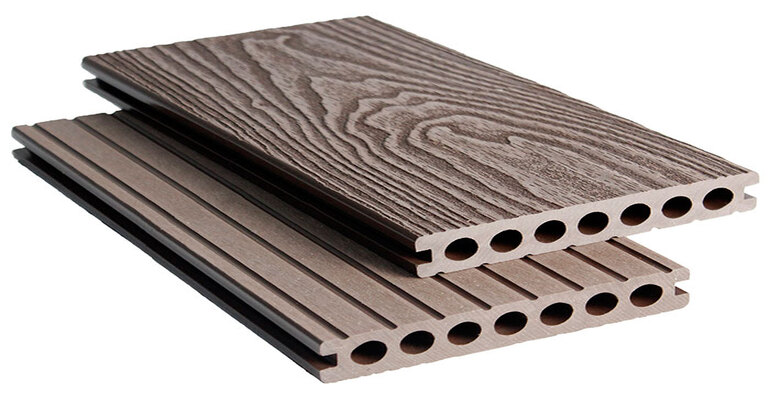
- Wood Component: The wood component in WPC typically consists of reclaimed or recycled wood fibers or wood flour. This wood material is often sourced from wood waste products, making WPC an eco-friendly choice. The type of wood used can vary, but the wood component must be processed into fine particles to blend effectively with the plastic.
- Plastic Resins: The other major ingredient in WPC is thermoplastic resins. Common options include polyethylene (PE), polypropylene (PP), and polyvinyl chloride (PVC). These resins provide WPC with structural integrity and enhance its resistance to environmental factors. The choice of resin influences the material’s flexibility, hardness, and other properties.
- Additives: In addition to wood and plastic, WPC incorporates a variety of additives. These include UV stabilizers to protect against sun-induced fading, fire retardants for safety, colorants to achieve desired aesthetics, and coupling agents to improve the bonding between the wood and plastic components. The selection and proportion of these additives are critical in shaping the final properties of the WPC.
- Production Process: Wood-plastic composite (WPC) is produced via a high-temperature extrusion process that melds wood fibers, plastic resins, and additives. The resulting mixture is shaped into decking boards, fencing profiles, or furniture components. WPC combines natural and synthetic elements, offering the aesthetic charm of wood alongside plastic’s durability, moisture resistance, and minimal upkeep.
This unique composition makes WPC ideal for diverse applications, including outdoor decking, furniture, and automotive and construction components. To harness the full potential of WPC in your projects, it’s crucial to grasp its intricate material composition.
Strength and Durability of Wood-Plastic Composite (WPC)
One of the remarkable qualities distinguishing Wood-Plastic Composite (WPC) as a material of choice is its strength and durability. WPC marries the best attributes of wood and plastic to create a robust, long-lasting material with various advantages for various applications.
- Load-Bearing Capacity: WPC exhibits significant load-bearing capacity, making it ideal for applications where structural strength is paramount. Whether used for decking, fencing, or structural components, WPC faces the challenges of supporting various loads, from foot traffic on a deck to the weight of outdoor furniture.
- Flexural Strength: The ability to bend without breaking is critical to WPC’s durability. This flexural strength ensures that the material can endure various stress conditions, such as wind loads on fencing, dynamic forces on automotive components, or the weight of individuals on outdoor furniture.
- Impact Resistance: WPC’s resilience against impacts is another testament to its durability. The material can withstand sudden forces without breaking or cracking. This quality is particularly valuable in applications exposed to potential impacts, such as outdoor furniture or playground equipment, where safety and longevity are paramount.
- Moisture Resistance: WPC’s resistance to moisture is a key factor in its durability. Unlike traditional wood, WPC doesn’t absorb water readily, reducing the risk of swelling, warping, and decay. This makes it an excellent choice for outdoor applications exposed to rain and humidity.
- Temperature Stability: Wood-plastic composite (WPC) boasts exceptional temperature resistance, maintaining its structural integrity from extreme cold to scorching heat. Its durability and ability to mimic natural wood have led to its widespread use.
WPC proves its value for year-round outdoor applications like decking and fencing or structural components in automotive and construction. It offers a blend of aesthetics and modern technology, guaranteeing long-lasting projects making it a top choice for those who prioritize longevity, strength, or both.
Moisture Resistance of Wood-Plastic Composite (WPC)
WPC boasts exceptional moisture resistance, making it a preferred choice for applications exposed to wet conditions. Unlike traditional wood, which is highly susceptible to moisture-related issues, WPC’s unique composition, combined with wood fibers and thermoplastic resins, fortifies it against the detrimental effects of water.
Moisture resistance is a vital attribute in applications such as outdoor decking, where the material must withstand rain, humidity, and exposure to the elements.
WPC does not readily absorb water; this innate resistance mitigates issues like swelling, warping, decay, and rot. This durability ensures that WPC maintains its structural integrity and appearance over time, even when subjected to high moisture levels.
UV Resistance of Wood-Plastic Composite (WPC)
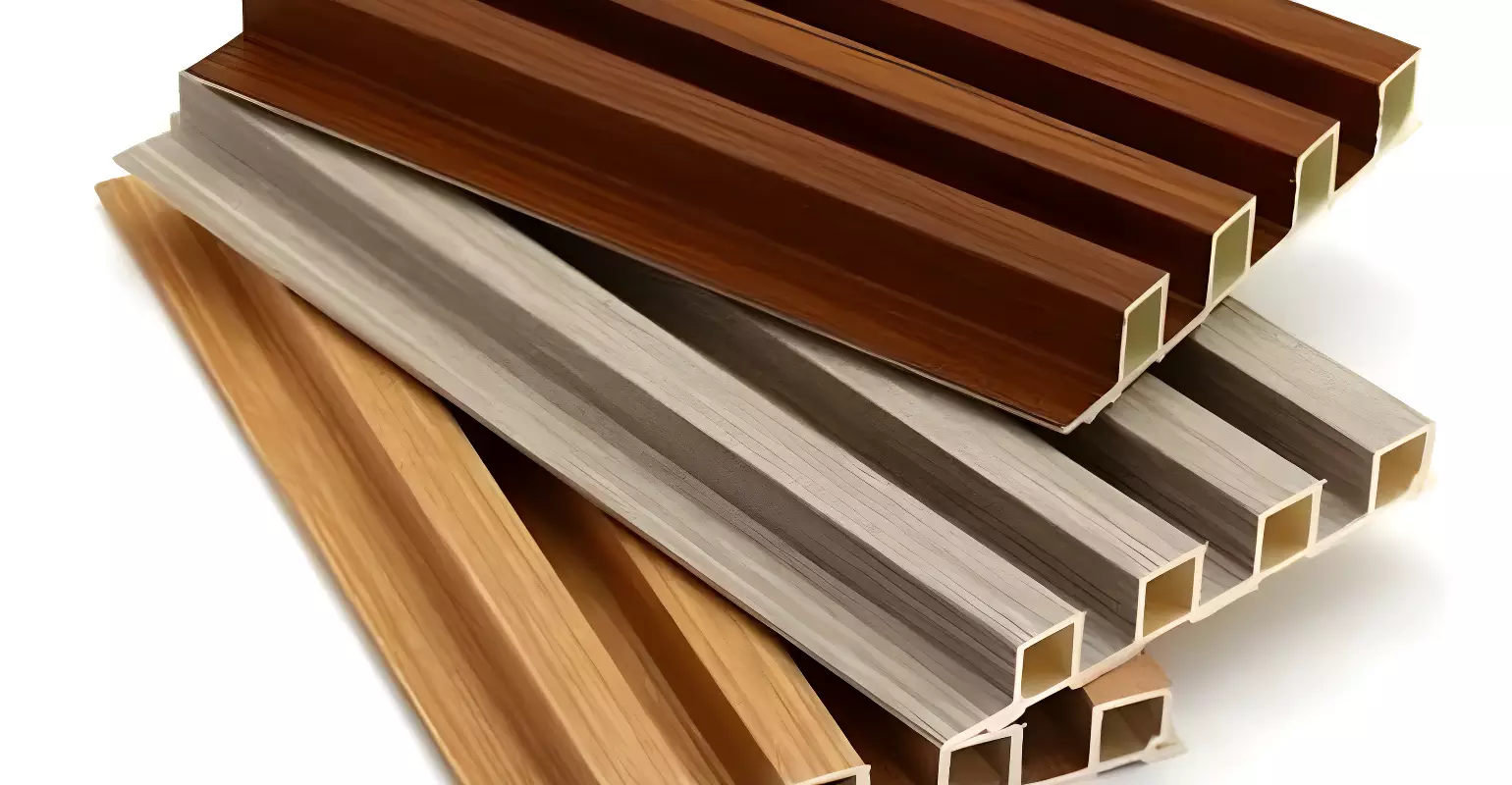
WPC’s ability to resist the damaging effects of ultraviolet (UV) radiation is a testament to its longevity and aesthetic appeal. UV resistance is critical, particularly in applications exposed to direct sunlight, such as outdoor decking, fencing, and furniture.
WPC products often contain UV stabilizers, which shield the material from the sun’s harmful rays, preventing premature color fading and surface degradation. As a result, WPC maintains its appearance over the long term, retaining its vibrant color and visual appeal.
Fire Resistance of Wood-Plastic Composite (WPC)
WPC’s fire resistance is crucial in applications where fire safety is a concern. Compliance with flammability standards is essential, particularly for indoor applications like wall cladding or components used in building interiors.
WPC products are designed to resist ignition and the spread of flames. Fire-retardant additives are often incorporated to ensure that WPC materials meet safety standards and reduce the risk of combustion. This fire resistance safeguards occupants and property, making WPC a safe choice for various applications.
Installation Requirements for Wood-Plastic Composite (WPC)
Proper installation is the linchpin of any successful Wood-Plastic Composite (WPC) project. Whether working on a deck, fence, or other application, adhering to specific installation requirements is essential to ensure your WPC structure’s longevity, functionality, and aesthetics. Here, we delve into the key installation considerations for your project’s success.
We also have an article about how composite decking is installed,Hope it helps you
- Site Preparation: Before installing WPC, prepare the site meticulously. Ensure the area is clean, level, and free from debris. Proper site preparation forms a stable foundation for your WPC structure and minimizes the potential for problems down the line.
- Substructure: The substructure is the skeleton supporting your WPC deck or structure. Use pressure-treated lumber or other suitable structural materials to create a sturdy framework, depending on the application. Following manufacturer recommendations and local building codes for the appropriate substructure design and materials is imperative.
- Handling and Storage: Handle WPC products carefully to prevent damage during transport and installation. Use appropriate lifting equipment for heavy components like decking boards. During storage, keep WPC products in a dry, well-ventilated area to prevent moisture absorption. Ensure they are covered and elevated off the ground to avoid contact with water.
- Installation Techniques: Follow the manufacturer’s guidelines and recommendations for fastening and spacing. Use recommended fasteners suitable for your specific application, such as hidden fasteners for decking or standard screws for fencing. Proper spacing, expansion gaps, and end-to-end fastening techniques are essential for functionality and aesthetics.
- Joist Spacing: Proper joist spacing is crucial for decking or flooring installations. Ensure that you adhere to the manufacturer’s recommendations. Correct spacing is vital for the structural integrity of the WPC structure and prevents sagging or bending.
- Slope and Drainage: For outdoor applications, such as decking, ensure your structure has the appropriate slope and drainage to prevent water accumulation. Proper water management ensures the longevity of your WPC structure and prevents issues like water pooling.
- Trimming and Cutting: Use the appropriate tools for cutting and trimming WPC materials. Ensure that you make clean, straight cuts to achieve a professional finish.
- Fastening at Ends: Pay special attention to fastening the ends of WPC boards to prevent splitting or cracking, which can occur in high-stress areas. Adequate fastening ensures the structural integrity and longevity of your project.By following these installation requirements and adhering to manufacturer guidelines and recommendations specific to your WPC product and application, you can ensure a successful project that functions effectively and enhances your structure’s overall aesthetics and safety.
Proper installation is the key to realizing the full potential of WPC and enjoying a lasting, beautiful project.
Safety and Environmental Standard Requirements for Wood-Plastic Composite (WPC)
WPC’s journey from concept to construction involves stringent safety and environmental standard requirements that prioritize both the well-being of users and the planet. Understanding these critical aspects is essential for all involved in producing, using, and disposing of WPC materials.
Safety Standards
- Toxicity: WPC materials should meet safety standards to ensure low toxicity levels. This is crucial for applications involving contact with skin or components used indoors, ensuring they do not pose health risks to users.
- Fire Resistance: Compliance with flammability standards is essential for indoor applications like wall cladding. WPC products often contain fire-retardant additives to reduce the risk of combustion.
Environmental Standards
- Sustainable Sourcing: Responsible use of wood fibers is essential. Ensuring the wood component of WPC is sourced from sustainably managed forests or uses reclaimed wood contributes to its eco-friendly profile.
- Recyclability: WPC’s eco-friendliness extends to its end-of-life phase. Designing products that can be recycled and using recycled materials in production further reduces the environmental footprint.
- Reduced Chemical Usage: Implementing processes that minimize the use of hazardous chemicals aligns with environmental standards and reduces potential harm to ecosystems and water sources.
Quality Control Requirements for WPC
Quality control is paramount in WPC production to maintain consistency, reliability, and safety. Here are some of the essential requirements in this domain:
- Raw Material Inspection: Ensuring the quality and consistency of wood fibers, plastic resins, and additives is a fundamental aspect of quality control. Thorough inspection and testing of raw materials are critical.
- Process Control: Monitoring the entire production process, from blending the materials to extrusion or molding, is crucial to maintaining product consistency. Precise control of temperature, pressure, and mixing ratios is essential.
- Random Sampling: Regular sampling of finished products allows for quality assessments. This approach helps identify any deviations from specifications and allows for adjustments in the manufacturing process if necessary.
- Quality Assurance Certification: Seeking third-party quality assurance certifications from organizations like Underwriters Laboratories (UL) or the Forest Stewardship Council (FSC) provides independent validation of product quality and adherence to standards.
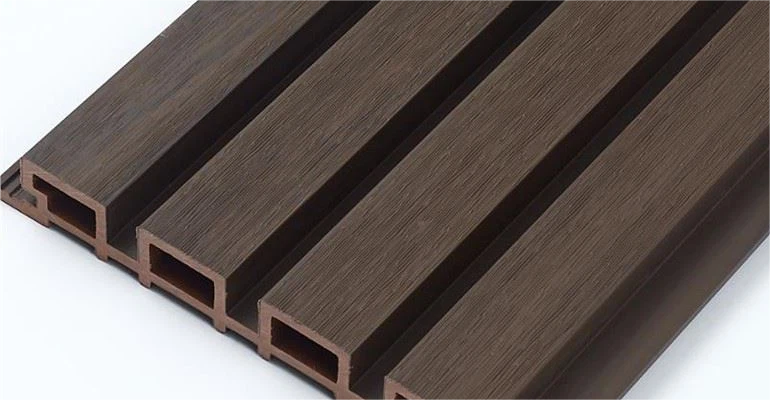
- Compliance with Industry Standard Requirements: Adherence to industry standards is a non-negotiable requirement for WPC. Various organizations and associations, such as ASTM, have developed standards for WPC production and use in different applications. Compliance with these standards ensures the products’ reliability, safety, and performance.These industry standards cover material composition, mechanical properties, fire resistance, and environmental impact. They act as benchmarks, guiding manufacturers and end-users to create and utilize WPC materials responsibly and effectively.
Conclusion
Wood-Plastic Composite (WPC) requirements establish its versatility and impact. From composition to durability, it defies traditional limits. Meeting safety, environmental, and quality standards safeguard users and nature. Quality control ensures consistency.
Adherence to industry norms promotes responsible practices. WPC combines natural aesthetics with modern precision, ideal for manufacturers and end-users. Embracing these requirements leads to innovation, sustainability, and enduring design.
Related Reading: What is the difference between WPC and PVC?
Jerry Kong
Dear Sir/ Madam
Does WPC suitable for vehicle driving on top?
And is it possible to apply nearby sea against salt resistance?
Thx